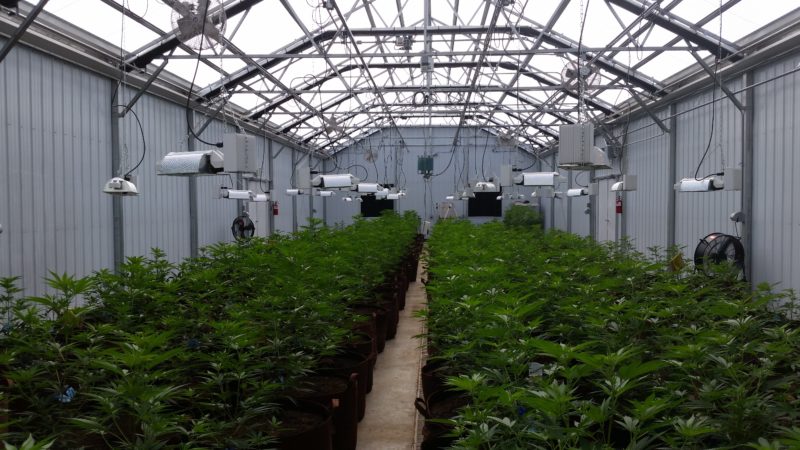
Transitioning to Cannabis
A plant is a plant. Many traditional horticultural growers have entered the cannabis market with that as their prevailing thought. While that basic concept is correct, the devil that is truly in the details has driven more than one operation to the brink of disaster.
A $2 mum and a cannabis plant, whose flower wholesales for as much as $4,000 a pound in some markets, are not the same. And treating them like they are is absolutely the incorrect approach. Every step of the process — from application, to building permit, to operational plan — is wrought with potential landmines that can derail a business before the first plant is ever grown.
This article will focus on the key facility and permitting questions that existing horticultural businesses have had to contend with across the country when considering jumping into the cannabis business.
RETROFITTING AN EXISTING FACILITY
When an existing greenhouse grower decides to take the plunge into the lucrative cannabis market — one of the first decisions that must be made is if they will use existing facilities and adapt them to grow cannabis, or if they will build a new facility specifically tailored to that crop.
Most existing greenhouse facilities are not set up to maximize cannabis production. There are several reasons for this.
For instance, cultural practices. With ability to blackout in flower phase being one of the most important features of any cannabis grow facility, this becomes an extremely problematic issue for an existing greenhouse. First, simply installing an overhead blackout curtain can be very difficult. Most greenhouses have a lot of overhead impediments that have to be dealt with. This can be everything from electrical conduit, to heat piping, to grow lights, to vent mechanisms. It also becomes extremely difficult to seal the blackout curtain to the end gables and sidewalls, and eliminate light leaks. As any grower will tell you — any significant light leaks in the flower phase can spell disaster for every plant in that zone. In addition, most large existing greenhouse facilities utilize natural ventilation as their primary cooling method. Th e key to all naturally ventilated greenhouses are roof vents. Adding a blackout curtain to this type of greenhouse will completely eliminate the greenhouses ventilation ability in key danger times for the cannabis plant.
These danger times are during the first few hours of blackout for a flowering plant during warm/humid summer months. This is the time the plant becomes most susceptible to humidity-related diseases such as powdery mildew, bud rot, etc. If the primary ventilation is above the blackout curtain, how can the zone be ventilated at plant level?
With the cannabis plant being extremely susceptible to humidity, most growers also prefer much tighter climate controls. From an existing facility perspective, this means:
1. Existing heating system may not be adequate. Under-bench hot water heating system is much more cost efficient, and also provides the grower with an additional cultural tool.
2. Existing environmental control system may not have enough functionality. Beyond sensors for temperature and humidity (which is common to all greenhouses), cannabis facilities also require them for light intensity, CO2, soil temperature, and soil moisture to operate at peak functionality.
3. Supplemental cooling and/or dehumidification may be needed in some climates. This can be problematic because miles of additional piping/ducting may be needed. Adding this to an existing greenhouse can be exceedingly difficult.
Another potential issue is that a cannabis greenhouse needs to have as tight pest controls as possible. Most states severely limit the crop protection tools that growers are allowed to use. In just about every state, these restrictions are tighter than they are even for vegetable production. If a solid pest screening system isn’t in place, it needs to be added. And this is very difficult to do effectively.
Lastly, most existing growing greenhouses use extremely large grow zones. Most of the systems (heating, shade systems, environmental controls, etc.) are set up that way. Cannabis growers prefer much smaller zones. There are multiple reasons for this. First, smaller zones allow them to isolate crops that are having disease and/or pest issues and not allow those issues to spread to the whole facility.
These small zones also allow for a more consistent harvest schedule, so that new flower product is available every week or two, not every eight- to 10-week flower cycle. This also provides for appropriate work fl ow for the harvest labor crew.
Most well-run operations also do a complete zone disinfection/cleaning after each harvest as part of their sanitation program. This is impossible to do if you are trying to use a perpetual harvest plan in a large zone. Building a new greenhouse facility provides a lot of advantages as all of the above listed issues can be avoided with appropriate upfront designs and layouts.
WHEN IS A GREENHOUSE NOT A GREENHOUSE?
It’s very important to note in most states agricultural exemptions to building codes have always been applied to growing greenhouses. But when it comes to cannabis, that is the exception, not the rule. Th e vast majority of states treat a cannabis grow of any kind — indoor/warehouse or in a greenhouse — as a manufacturing facility. Very few treat them as an agricultural facility.
This means existing horticultural businesses must be prepared to deal with code issues that they have always been exempted from. These not only apply to new builds, but since even a retrofit of an existing greenhouse will need a building permit — they very well may apply to those as well.
Some of the major issues are:
Fire code. Generally speaking, most commercial buildings over 10,000 square feet are required to have fire suppression. Growing greenhouses have historically been exempt from that requirement. But if you plan on winning a cultivation license, include fi re suppression in your budget. The issue this potentially causes for existing greenhouses is the structural dead load. If your greenhouse was built using all agricultural exemptions, it most likely does not carry enough dead load to take on the additional weight of a fire suppression system.
So you could potentially be looking at significant additional cost to upgrade that loading. And because many times the original blueprints and loading information are not available for an older greenhouse, this process can get very sticky.
The greenhouse will need at least a stamp from a state-licensed engineer, certifying that structure meets local code for wind and snow load. Most engineers are not willing to put their reputations on the line based on existing load guestimates. And if they are, you can be sure that the cost for them to do so will be significantly higher than expected.
Of course, a new greenhouse grow facility can be designed from the start to meet all codes, including the dead load required for fire suppression.
Energy code. Greenhouses have usually been exempted from the national energy code. After all, any light-transmitting roof covering is going to have a very low r-value. The more light transmission a covering has, the less heat retention it provides.
Many licensed cannabis growers building a new facility have run up against this issue with local code officials. In a vast majority of cases, the growers have won the argument. But not until a lot of time, energy and money were spent. And in the cannabis industry, time really is money.
Zoning. If an existing facility is in an area that is zoned for agriculture, will that apply to a cannabis facility? If you are building new on a new piece of property that is zoned for manufacturing, there are potentially a whole new set of issues that may have to be dealt with. A few of these include: facility appearance, environmental regulations, set-back requirements and waste water handling.
BUILDING A NEW FACILITY
Building a new cannabis facility also is not without its challenges. Many of the issues already discussed also apply. However, it is much easier to avoid those pitfalls with strong pre-planning. This includes working with an experienced greenhouse provider who has done a large number of cannabis grow facilities in your state.
In addition, any good greenhouse provider can provide a recommendation on a quality architect who has experience in cannabis facility design. This experience will help avoid common pitfalls, and in the long run, save you time and money.
There is a whole checklist of important issues to consider when building a new facility. These should all be considered as you move forward.
Are there special local approvals needed just to build a cannabis facility in that city, town, municipality? In Michigan, for example, a potential cultivation licensee must have local approval before they can even apply to the state to be part of the program. Many local legislative authorities have banned every type of cannabis facility in that state.
Many states have strict rules on how close any cannabis facility can be to a daycare, school or church. These should be reviewed closely to ensure the property is in compliance.
Odor control is an extremely important issue to research. Are there regulations written into the state or local code? Is the facility going to be close to residential property? Residents can cause you significant headaches, even if there is no code requirement related to odor.
Some styles of greenhouse can be fitted with odor mitigation equipment, and others cannot. This is where working with a qualified greenhouse provider becomes vital. Multiple operations — both greenhouse an indoor — have run into odor issues with local residents if they have not dealt with it properly up front.
Beyond that, there are many construction-related questions that must be determined before a piece of property should be acquired:
1. Is there currently enough electrical service available on that property — both for this first build as well as potential expansions? Is three-phase service available?
2. How about water for irrigation? Are you on city water, or is there a well? If there is a well, does it provide enough volume? A water test is also a good idea for well water to determine how much, if any, treatment will be needed to make it appropriate for the plants.
3. A firm should be hired to conduct borings and soil tests to determine not only if there are contaminants present, but also what lies below the surface. This could affect your ability to use a foundation in your build.
4. It will also need to be determined if you will need a retention pond for the rain water off the roof. Depending on how large your greenhouse facility will be, you may need to dig a pond on the first phase. Or you need to allocate that space if you plan on future expansion.
5. The architect should do a local code review before land is purchased to make sure there are no surprises, such as the set-backs, landscape/appearance requirements, etc.
6. A security plan should be put in place early in the process. It’s important because you will probably be required to have a perimeter fence as part of that plan. This can take up some valuable build space.
If you are an existing horticultural grower, there is no doubt an extremely high revenue crop like cannabis seems very attractive. Just make sure you are going into it with your eyes wide open, because in this case, beauty is truly in the eye of the beholder.