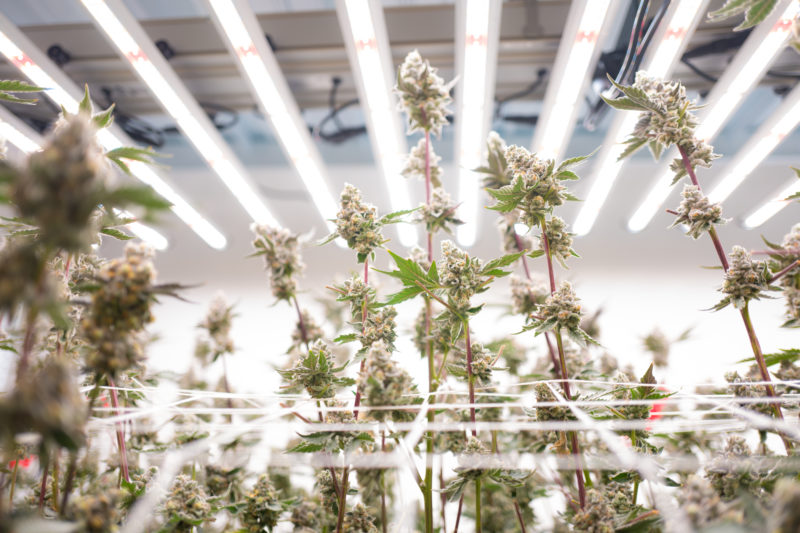
The Cannabis Conundrum
If you are a grower of ornamental crops interested in producing cannabis, be aware there are a lot of unknowns about producing, harvesting and processing this crop.
“For ornamental crops, the research literature provides a wealth of information related to cultural practices including fertility, light intensity and other factors,” says Allison Justice, vice president of cultivation at OutCo in El Cajon, California. Justice, who has been with the cannabis production and wholesale/retail company for two years, received her PhD in plant and environmental science from Clemson University in 2014. OutCo has been operating since 2015 and produces cannabis for both medicinal and recreational sales.
“The biggest problem I experience with producing cannabis, even after working with the crop for two years, is the lack of a baseline,” Justice says. “If I was growing poinsettias, there is a baseline of nutrient concentrations that are used. If a tweak needs to be made in the nutrients, it’s easily made.”
not making a fertilizer solution where they know what their inputs are. They are using a ‘brand’ and in many cases the fertilizer labels are wrong or misleading.”
Justice says cannabis growers trying to make decisions on how to tweak their nutrient solutions have to really do some major work to have their fertilizers analyzed.
“Most cannabis growers don’t even know what nutrients they’re using,” she says. “Th ey know they’re using vegetative A and B and then switching to flower A and B. Th ere is no baseline for fertilizers of knowing where to start. This not only applies to nutrition, but also light levels and pest and disease control. There is no true baseline available from universities or even other cannabis growers who can assist growers in making their own in-house assessments.”
When Justice began working at OutCo, it didn’t take much effort to make simple improvements.
“I removed 500-gallon tanks fi lled with diluted fertilizer,” she explains. “These tanks were mixed nearly every day. The tanks were replaced with Dosatron injectors. I made little improvements that 99 percent of ornamental and vegetable greenhouse growers have been doing for a long time. Unfortunately, these kinds of improvements haven’t been made yet by many cannabis growers.”
“I have found it is much harder to make improvements in the cannabis industry than any other ornamental company I have worked for just because the rationality behind how some of the things are done. There has been much resistance to change in how cannabis is produced.”
MINIMAL POSTHARVEST INFORMATION
Justice says that while good production information on cannabis is lacking, she has found even less information available on harvesting and processing cannabis.
“When I arrived at OutCo I found everyone had their own ‘artistic’ method of drying and curing,” she says. “My greatest passion right now is figuring out what is occurring with cannabis during drying and curing. There is so much to these processes. I’m reading papers related to cut flower postharvest and the harvesting of tobacco. I also have read about the curing of wine and what happens to it with certain processes.”
“You can grow the perfect looking cannabis crop, but if it isn’t dried and cured correctly the product could be ruined. If dried improperly, Botrytis could ruin the crop. If dried too quickly, all of the terpenes could volatilize leaving a product that smells like hay.”
OutCo is focusing on how to best process the harvested cannabis plants.
“We are approaching this by trying to figure out what is going on with the plants,” Justice says. “When we’re drying the plants, I call it this ‘zombie’ state we’re trying to keep the plants in. We’re drying the plants slowly so we don’t evaporate all of the terpenes so the buds continue to smell nice. Yet, we don’t want microbials to grow and damage the buds. It is a very delicate process that we are still learning about.”
SIMILARITIES TO ORNAMENTAL CROPS
Whether cannabis is grown in a greenhouse or indoor grown, there is no real diff erence in how the plants are harvested and processed.
“The end goal when harvesting cannabis is the flower buds,” says Fred Green at Fred Green Consulting in Princeton, Massachusetts.
Green, who grew cut flowers for 30 years, has transitioned from ornamental crop production to assisting companies looking to enter the cannabis industry. He has consulted on the design and operation of warehouse and greenhouse cannabis production facilities in Massachusetts, Alaska, Colorado, Maryland, Washington, Canada and Australia.
“Growing cannabis is almost identical to growing mums,” he says. “If growers know what goes into growing mums, then they should have a good sense for what goes into growing cannabis. With cannabis it is very strain dependent. At the same time, there are different cultural practices that can be used.”
He adds, “Just like with greenhouse ornamental crops, I’m all about turns or how many crops a year can be produced per square foot. In my experience, a grower is better off turning the crop more frequently and harvesting less product per crop. At the end of the year, the grower who produces six cannabis crops actually ends up with 20 percent more product per square foot than if only four crops of larger plants were produced.”
Green says some growers prefer growing larger plants and fewer crops because of the labor involved with handling more crop turns.
“The growers who produce these large plants, one of the reasons they do it this way is they do everything by hand so they have to handle fewer pots,” he explains. “That way they only have to fill pots four times a year instead of six times a year. However, cannabis growers who have automated their operations with conveyors, pot fillers and carts, will produce more useful product per square foot by doing more crops than fewer crops.”
SANITATION IS CRITICAL
Green says the sanitary conditions for harvesting cannabis should be as strict as the harvesting of any other edible or medicinal crop.
“In the case of medicinal cannabis this is supposed to be pure medicine so it should be treated that way,” he says. “Good cannabis growers have their trimmers dip their clippers in alcohol every five minutes. They wear hair nets and rubber gloves. I also suggest to my clients that their trimmers should not have any facial hair. Harvesting containers should be cleaned out at the end of the day.”
Green says operators who have not implemented these sanitary practices are out of business or they are being shut down because the regulations are demanding more sanitation and quality control.
AUTOMATING HARVESTING
Green says the large fan leaves and stems of cannabis plants have very low value. However, the small leaves, called sugar leaves, that surround the buds are quite valuable. They are called sugar leaves because they frequently have many white trichomes on them, which contain cannabinoids.
“The sugar leaves look like they have a dusting of powdered sugar on them,” he says. “Consumers can buy dried sugar leaves, but most growers trim off these leaves and use them for making what the industry calls ‘pre-rolls.’ These pre-rolled joints enable growers to move material that is not as in demand as the dried buds, which are what most people want.”
Green says cannabis growers who are focused on producing higher crop volumes are increasingly automating their operations.
“These high volume growers are using trimming machines which are quite good at handling the buds,” he says. “When these trimming machines were introduced five years ago, they really beat up the buds and caused a lot of damage, especially to the trichomes. Now hand trimming and machine trimming are very close. Only experienced growers can tell the difference between hand-trimmed and machine-trimmed buds.”
According to Green, an experienced trimmer can trim 1 pound of buds in an eight-hour day. Trimming machines, which cost $8,000 to $10,000, can handle up to 3 or 4 pounds an hour.
“I did a comparison study of machine-trimmed versus hand-trimmed buds for one of my clients and the machine-trimmed labor budget was $80,000 for the year,” he says. “If the same volume of buds was trimmed by hand, the labor budget for the year was $900,000. Looking at this from a business standpoint, how many customers really care or even really know whether the product was trimmed by hand or by a machine.”
“I expect 90 percent of consumers would pay the same amount for machine-trimmed product. For those consumers who are adamant about purchasing hand-trimmed buds, I advise growers to trim 80 percent by machine and the remaining 20 percent by hand and charge more for the hand-trimmed product. Growers know which of their customers are more selective. These customers could be charged 20 percent more for the hand-trimmed product.”
Green says more equipment to automate the harvesting and processing of cannabis has been developed, including deleafing (bucking) and bud grading machines.
PROPER DRYING
Green says the biggest challenge with drying cannabis is ensuring uniform drying across the bud.
“There is this big wide bud, which is solid and very dense,” he says. “If the conditions are not right, the outside of the bud is going to dry out and the inside of the bud is going to still be moist. This could result in the bud rotting from the inside out. If the buds are dried too slowly sometimes they will rot. It is a challenge to provide the right parameters to obtain the proper moisture level.”
Justice says OutCo has conducted studies to determine the best temperature and humidity levels for drying the buds.
“We have found through our research that a 60 percent relative humidity and 60° F work well,” she says. “This prevents the terpenes from evaporating and lowers the moisture level fast enough so damaging microbials won’t continue to grow. At these levels the plants dry slow enough so they stay in that ‘zombie’ state where enzymatic activities can continue to occur such as chlorophyll degradation and the conversion of starch to sugars.”
Green says some growers, who are less automated, hang cannabis stems upside down on wires to dry as soon as they are harvested.
“These growers believe there are compounds in the leaves that drain down into the buds,” he says. “They believe higher levels of cannabinoids, terpenes and flavonoids collect in the buds if the leaves are left on while the stems are drying.”
Green says some growers who are handling large quantities of buds are using rolling racks equipped with perforated trays that are easily moved into temperature- and humidity-controlled drying rooms. He says growers should work with engineers who have experience designing and building drying rooms for cannabis. He recommends growers who are doing weekly production to build two separate drying rooms. This will allow growers to sterilize one room while the other one is in use.
“After the finished product is removed from the trays they can be rolled back into the drying room for sanitizing,” explains Green. “The floor is swept and the grower can use something like a Dramm Autofog to sanitize the room with a broad spectrum bactericide/fungicide such as ZeroTol or OxiDate. Some growers pressure wash the racks and room, but this isn’t necessary. Growers should sterilize the racks, equipment and drying rooms between every crop.”
“When the buds are first rolled into a drying room, there is going to be a lot of moisture. A cooler temperature (65 to 68° F) is generally better for drying. Initially the dehumidification should be a little higher. The end goal is to lower the moisture content in the buds to about 15 percent. If the dehumidification system is turned up too high, the outside of the buds can dry out and become shriveled and fall apart. The inside of the buds will also be too wet. The goal is to slowly draw the moisture out so the buds are uniformly dry from the outside all the way to the inside. Too much air circulation can dry out the outside of the buds and not the inside.”
Green says another method of drying is to use laminar airflow with supply ducts on one side of the drying room and return ducts on the opposite wall. The air moves from side to side rather than from floor to ceiling or from ceiling to fl oor.
For more information: Contact OutCo, 619.448.4420, ajustice@outco.com or Fred Green Consulting, 508.395.6321, fredgreen@sprintmail.com.