
Affording to automate in the greenhouse
According to USDA-Economic Research Service, wage and salary employment in agriculture, including horticulture, has been on a gradual upward trend since 2010. Agriculture employment has risen from 1.13 million workers in 2013 to 1.17 million in 2023, an increase of 4%.
The 2022 Census of Agriculture indicated that wages and salaries, plus contract labor costs, represent just 12% of production expenses for all farms. However, these costs account for 42% for greenhouse and nursery operations, and 40% for fruit and tree nut producers. Most hired ag workers are wage and salary employees, hired directly by ag producers. Some of these workers are also employees of agricultural service companies, including labor contractors and management service providers.
Over the past five years, USDA’s National Agricultural Statistical Service Farm Labor Survey has shown that real farm wages have grown 2.1% per year. By 2023, the average farm wage ($17.55) was equal to 61% of the nonfarm wage ($28.93) indicating the gap between farm and nonfarm wages is slowly shrinking.
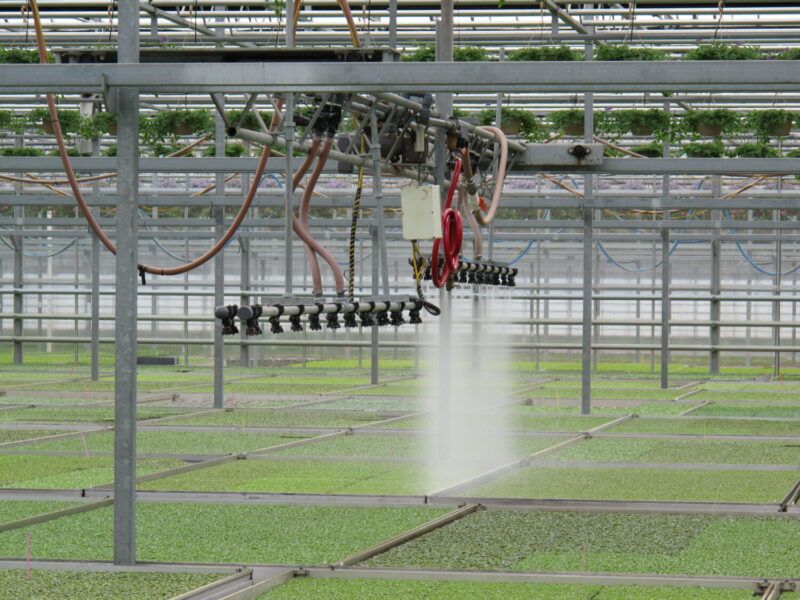
REASONS TO AUTOMATE
It is becoming increasingly difficult to find and retain labor within many industries.
“In the ag industry, including horticulture, it is challenging to find people who are willing to do physical work under sometimes challenging working conditions,” said A.J. Both, controlled environment engineering professor at Rutgers University. “This is one of the main reasons that companies are looking at automation.
“In some cases, it is the cost for that labor — how much growers have to pay to find workers who will work for them. It’s not just the pay; in many cases, it’s also the benefits that are offered. These can add up quite quickly.”
Growers are looking at the tasks workers do and how they work. They have observed and also have experienced that some jobs are tedious and repetitive. Automation can help to remove some of the tasks that workers don’t like to do.
Ag economist Michelle Klieger, president and founder of Stratagerm Consulting, said when she talks to growers about whether they should automate, they are either trying to save money or increase production.
“Automation can allow growers to save in labor costs more than the cost of the equipment,” Klieger said. “Automation can also increase production, allowing growers to sell more than the cost of the equipment. If a cost-benefit analysis shows that automation will enable a grower to end up in a better place financially, it is an easy decision to purchase a piece of equipment.
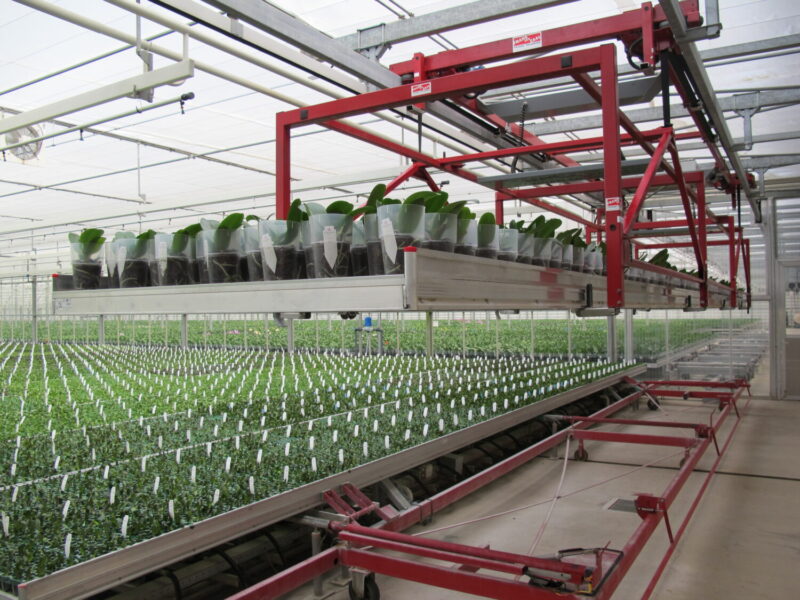
“Growers are looking to do more with the labor they have or [wondering] how they can reduce the demand for labor if it is not available or, in a lot of cases, if the labor is too expensive.”
Another factor growers may not consider, Klieger said, is when the risk to a crop is high.
“Automation can be a form of protection,” she said. “A greenhouse equipped with temperature sensors and environmental controls can protect the plants automatically without anyone having to constantly be monitoring the temperature to ensure the plants are protected. If this equipment isn’t installed, there is a high risk the plants could be damaged or completely lost.
“In this case, automation can be critical to providing growers with an opportunity to protect their investment and against the risks that they may not always be onsite to handle.”
OBSTACLES TO AUTOMATION
Investing in automation can be a major challenge when finances are tight. Growers must weigh the benefits of the investment vs. the savings that will be realized by installing the equipment and eliminating the manual labor that would be used to do an activity.
“Expense is a big reason why growers don’t automate,” Klieger said. “If a grower can move X number of transplants per hour and reduce labor by one person, that calculation makes sense when it’s possible. Making that calculation can be difficult to do because, in many growing operations, workers are doing more than one task or the return on investment just isn’t obvious.
“Another issue, especially for small growers, is they don’t count their time or family time in their operation costs. They don’t account for the cost of their own time and the impact on their quality of life. The money coming out of the checkbook is more important than the extra hour of work a day, even when most people who support the industry will tell growers this has to be a sustainable job for them as well.”
Klieger said regardless of the type of automation a grower is looking to install, whether it is environmental control or task-focused, it comes with a cost and the pressure of taking out a loan and having to pay it back. Even though automation might make a lot of sense, growers are likely to still have a big financial outlay.
Another consequence of automation may be the need to redesign workflow.
“When workers are involved and the workflow has to be changed, people may be taken out of the equation and replaced with automation,” Both said. “Redesigning the workflow can sometimes be a challenge that requires some thinking and adjustments that may not always be as straightforward as people may think.”
Another challenge growers may face when installing equipment is having it serviced, especially if it comes from overseas.
“There is quite a bit of equipment manufactured in Europe being used by American growers,” Both said. “While that equipment is designed well and works well, eventually it will need service. To obtain replacement parts and hire the service people who know how to make equipment repairs onsite and in a timely manner is not always that easy.
“In the ag industry, including the controlled environment sector, growers are very resourceful and like to work on equipment themselves. A grower or someone on their staff may have the skills and experience to service equipment. However, with more technical automation equipment that may not always be possible. Some of the equipment has gotten very complicated or requires specialized tools to do the maintenance and repairs.”

FILLING A NEED FOR AFFORDABLE AUTOMATION
When Max Knight started a vertical farm to grow microgreens in 2021, the operation included a lot of technology-related automation that was designed and built in-house.
“We were not only trying to automate more of the tasks but also trying to automate in a way that was far more cost-effective than what was available for the vertical farm industry,” said Knight, co-founder and CEO of Rooted Robotics. “We operated the farm until 2024, when we rebranded and decided to focus on selling some of the technology we had developed to other growers. We reworked a lot of our equipment designs to make them more suitable for the broader CEA market.
“As I got more involved in the industry, I realized many indoor farms were struggling in terms of profitability. For most of these farms, I found labor costs were the biggest issue. That’s why we decided to focus on robotics. I had studied engineering in college, so this was kind of in my wheelhouse to develop this kind of technology.” Another reason for the switch from growing to designing and building his own equipment was the high cost of automation on the market.

“Being that we were operating a small facility, it didn’t make sense for us to spend $50,000 on one machine that only does one process,” Knight said. “This is why we ended up developing our own equipment and then pivoting to manufacturing and selling it to other growers who were encountering this same issue.”
The first piece of equipment available from Rooted Robotics is for microgreen growers producing in 1020 plant trays.
The company is also designing and building equipment that will work with nutrient film technique channels and floating raft systems used for a variety of crops. The company has focused on three different processes: planting microgreen seed, harvesting microgreens, and washing 1020 trays and NFT channels.

“Each of these processes we have identified from our experiences as well as the experience of our customers,” said Eric Roth, who is the company’s COO and an experienced microgreens grower for more than 10 years. “Those are three of the biggest pain points we see across the board in all these indoor farms. The biggest labor steps are seeding, harvesting and cleaning the trays.
“Our equipment is small, fits into any size operation, and can easily be moved and stored,” Roth said. “A lot of vertical farms are small — 700 to 1,000 square feet — with growers trying to produce as much as possible in that space, but they want to install some type of automation.”
He said offering equipment that has mass adoption potential and incorporates industry standards is good.
“There are too many custom production systems on the market, and standardization is a huge part of how we can lower the cost of automation,” Roth said.