Managing vapor pressures in controlled environment agriculture
Plant growth reacts positively or negatively to the vapor pressure deficit (VPD) — the difference between the leaf vapor pressure (LVP) and the surrounding cultivation room vapor pressure (RVP). It begins with the release of water vapor through tiny pores on the leaves called stomata.
Low vapor pressure surrounding the leaf pulls water upward through the plant. The vapor pressure difference, the VPD, is the force that governs water movement through a plant and results from deducting the RVP from the LVP.
The CEA industry continuously seeks to improve a crop’s outcome. However, within the realm of climate control for plant life, advancing the key factor of canopy ventilation (CV) gets little attention.
Without adequate CV, heat and humidity get trapped in the canopy foliage. The entire process improves when the heat and humidity are driven from the canopy foliage and processed by the HVAC system.
Cultivating room vapor pressure is a fixed value based on temperature and relative humidity (RH). LVP is a function of the leaf surface temperature (LST) and RH. The RH of the leaf is always 100% because of continuous transpiration. Therefore, the LST is the sole variable that controls the VPD.
LSTs are a function of the lighting intensity, air temperature and air velocity surrounding the leaf. Artificial lighting used to promote photosynthesis gets carefully distributed to ensure uniform exposure on the canopy. To be effective, there should be a uniform distribution of CV.
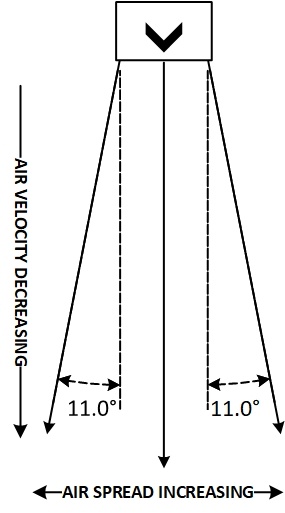
CV involves more than just blowing air at the foliage. Surprisingly, the most challenging engineering task to control VPD is designing a CV system that uniformly frees heat and humidity from the foliage. The design of this system should be part of the early design phase.
Collaboration is essential between the HVAC engineer, cultivator, and any third party involved with the design of the structure that houses the plant lighting and irrigation system.
The current protocol for CV entails design by a cultivator, who is usually inexperienced in airflow dynamics. This results in a haphazard array of ducts weaved throughout the structure, or fans blowing air at the canopy, while leaving sufficient room for maintenance.
Ducts or fans must not block light waves or otherwise cast shadows that interfere with photosynthesis. Plant architecture teaches that water vapor discharges from the stomata on the leaf surface while radiant light waves heat the leaf surface. Temperature and water vapor hug the leaf’s surface, forming a thin boundary layer.
To manage the VPD, the ventilation system must continuously provide turbulent air to disturb this layer by sending heat and humidity into the cultivation room for processing through the HVAC system. This requires a CV system that provides sufficient and uniform air turbulence inside the canopy.
There is no definitive advice about the air velocity needed in the canopy. It may depend on the type of plants and environmental conditions. However, current practices propose an air velocity of 40-100 f/m, which translates to a minimum of 40-100 f3/m/f2 of canopy.
In contrast, a light outdoor breeze has an air velocity of 300- 600 f/m. Regardless of the actual requirement, the air volume for CV is likely to be significantly greater than that needed for HVAC.
Ventilation air is separate from the air needed for temperature and humidity control. The CV system provides sufficient air velocity throughout the canopy and keeps the LST close to room temperature, while minimizing excess ventilation.
Light waves that serve photosynthesis also emit radiant heat to the leaf surfaces. CV cools the leaf surfaces, which prevents heat buildup and lowers the LVP and VPD. Canopy air volume and velocity govern the ability of ventilation air to penetrate the foliage and cool the leaf surfaces. Too much velocity is better than too little. However, the ventilation system cost and efficiency benefits from velocity that is “just right.” The designer finds the happy medium through trial and error, mixed with experience and some imagination.
Figure 1 shows that airflow spreads as it moves from its source, covering a wider area while the velocity diminishes. The natural spread angle is approximately 11° in all directions and is roughly one unit of spread per every three units of throw. This rule is true regardless of the angle.
Figure 2. Parallel airflow results in a significant portion of air velocity missing the canopy.
Figure 3. With airflow perpendicular to the canopy, overventilation is unnecessary.
We recommend using the perpendicular airflow (Figure 3). Hybrid-angle airflow (Figure 4) is acceptable, but parallel airflow (Figure 2) is unacceptable because it results in a significant portion of air velocity missing the canopy. The symbol > illustrates the source of airflow, which is connected to a recirculation fan or air ducted from outside the canopy.
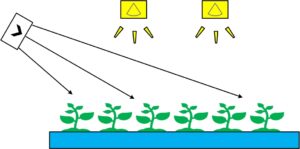
Perpendicular airflow, as shown in Figure 3, demonstrates the most efficient method for achieving CV. With airflow perpendicular to the canopy, overventilation is unnecessary. The distance from the air delivery source to the canopy is uniform and achieves adequate ventilation in the far-reaching areas. Here, all the canopy areas will have a near equal LST, and the air is 100% effective for ventilation.
Compared with the method of Figure 4, the total air volume is significantly lower. However, overhead space for ductwork is required to deliver ventilation air from outside the canopy.
The distance between lighting and canopy varies depending on the crop and the stage of growth. When ventilation airflow is perpendicular to the canopy and at the level of lighting, as in Figure 3, there is a short and uniform distance from the air source to the canopy.
The primary rule for efficient ventilation is to design a system with uniform distance between the air source and the canopy it serves, with sufficient velocity to penetrate and effectively ventilate the canopy.
Hybrid-angle airflow, as shown in Figure 4, offers an acceptable method for achieving CV. The traveling distance to the farthest point is greater, so we need to provide over-ventilation closer to the source to ensure adequate ventilation to the far-reaching canopy areas.
Over-ventilated canopy areas will have a lower LST compared with the remote areas. However, with sufficient initial velocity, the difference between LST near and far minimizes, with less effect on the VPD.
LSTs have a potential minimum, but no maximum value. The potential minimum value is just short of the ventilation air, temperature serving the canopy. However, there is no limit to how warm the leaf surface can get without sufficient ventilation air. Therefore, excess ventilation is preferable.
It is necessary to originate a portion of ventilation air outside of the canopy and duct it into the canopy, as illustrated in Figure 5. This will drive heat and humidity from the canopy into the aisles and avoid recirculation within the canopy.
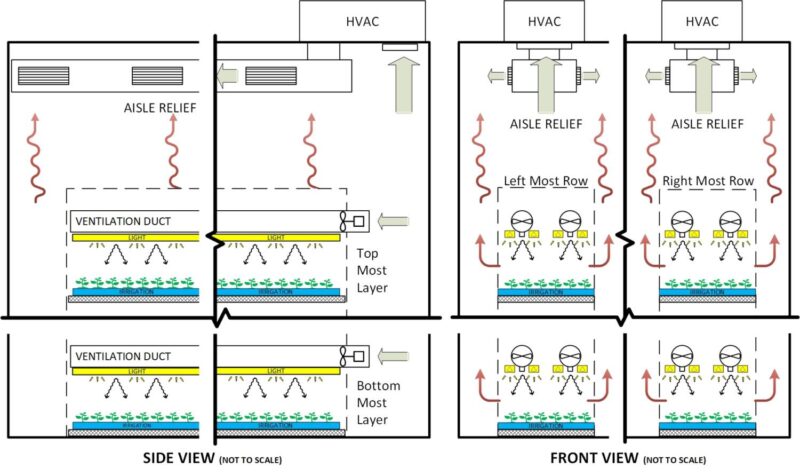
We cannot underestimate the importance of CV for managing vapor pressures in CEA as it is significant. This article outlines the best general practice for distributing air in a canopy. However, we need research to establish air velocity and volume rates for diverse crops with different canopy densities.
CEA facilities have conducted trial-and-error efforts, but there is very little documentation on this topic with CEAs. This is clearly a complex endeavor.