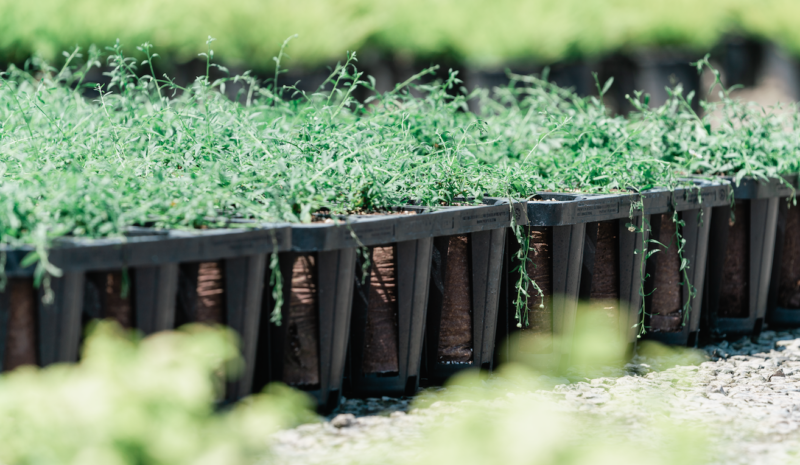
A Solution for the Future
As growers, we have many day-to-day activities that must be taken care of, so we don’t always look at longer term projections. One of the greatest issues our
industry faces is the vehicles we use to present and grow our plants in: the plastic pot.
It all started back in the 1960s when the vehicles used then were steel cans and clay pots. The plastic pots were cheaper and more convenient to use. They could be stacked and didn’t break when handled; it didn’t take long for our industry to shift full on into using them.
Present day 2019, almost 60 years later we are seeing the repercussion and damage of the environment of using so much plastic products in our society.
Those of us in the nursery and greenhouse industries have always considered ourselves the “green industry,” but in reality we know that is not the case. We create lots of waste streams with our products, most of which will not be recycled. It is estimated of all the plastics we buy our products in, 90% will end up in the landfill or our oceans. That’s including all the plastic pots we grow our plants in.
WHERE TO NOW?
We are at the crossroads on how we move forward to address this challenge. I’ve been working with Ellepot USA to help them develop large ellepots for the four segments where plants are sold through: landscapers, retailers, agriculture and recently the cannabis segment.
A few leading nurseries such as Sierra Gold and Sunridge Nursery have already addressed the plastic pot issue by not shipping the trees or vines in pots. Their technique of shipping just the plants in the ellepots serves multiple purposes:
1. Trays don’t leave the nursery to get lost, damaged or contaminated and can be reused up to 15 years depending on the tray design.
2. Drivers don’t have to return to the farms to pick up pots, eliminating driver time and fuel.
3. The contractor who plants the trees or vines doesn’t have to dislodge the plants from the plastic pots, avoiding root damage, but more importantly saving time on transplanting — as much as 10% along with no cleanup of pots afterward. This savings alone can add up to hundreds of thousands of dollars in labor savings. Another benefit to the ellepots is fewer losses in the field due to better roots structure. Have you ever calculated the cost of replanting liners in your operation?
The large ellepots that were originally designed for the agriculture industry could be used in the ornamental industry. Benefits include better root systems, better transplanting for the consumer, smaller hole to plant in and the reduction of plastic pots to dispose of. Through trials we’ve found we can create a better root system with a smaller diameter plant, saving the grower up to 20% less media along with putting 20% more product on the trucks during shipping.
Another area Ellepot USA and Proptek are working on is the movement of people to the plants — or I should say “Plants to the People.” In doing a cost analysis based on our future California minimum wage of $15 an hour along with taxes and workers’ compensation insurance, the true cost per hour raises to $18.60 or 31 cents per every minute. Depending on how many employees you have, those minutes of people walking back and forth to the job can add up substantially. Remember each minute is costing you 31 cents.
Ellepot USA and Proptek are designing systems where the trays can be moved by forklifts and carry multiple plants with one single forklift operator. It’s not new technology, but based on the systems developed in Europe. So instead of handling one tray of large ellepots one by one, a forklift operator can move up to 24 trays at one time. Though the initial cost to set up seems high, do a job/time analysis and see how much time each job takes and multiple that by 31 cents. It will be shocking.
Within the agriculture, landscape and cannabis segments the presentation is not an issue. They don’t care about seeing the paper, but at retail we are working on making the large ellepot a little more visually appealing. We have come up with a wrap with graphics that can last for a few weeks under retail conditions. This presentation is a reduction of 96% less plastic than a plastic pot.
I know it’s not easy to change but, just like hybrid cars that were introduced 20 years ago, the time to think about change is now. We are reaching a tipping point in the way we have done things and we must now think about trying to create the lowest impact while growing and selling our plants.