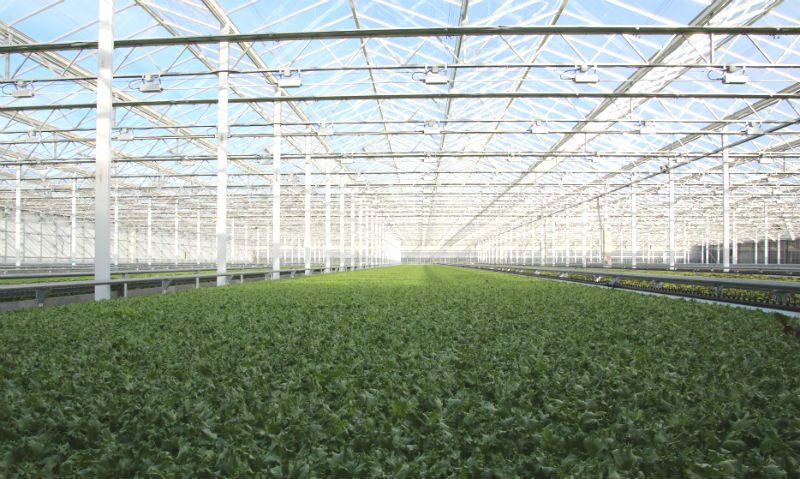
High Tech Growing Systems Help Improve Efficiencies, Meet Consumer Demand
Most young boys dream of growing up to be firefighters or policemen. But others, like Tero Rapila, grew up in Finland and spent their summers dreaming of designing a less labor-intensive way to toil in the family-owned greenhouse. There was certainly plenty of time to ponder an easier method during the long afternoons as he hand-seeded, watered, transplanted, harvested and packed lettuce.
Eventually, together with his uncle, they developed the first automated growing system for the greenhouse. Later, after his subsequent studies of engineering and a career with a leading industrial automation company, Rapila and his friend, Juhana Kantola, founded Green Automation Export in Finland.
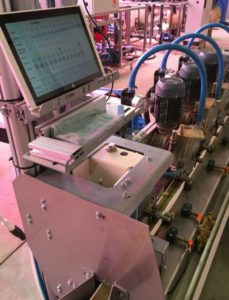
Cut to present day, Rapila, chief executive officer, and Kantola, chief technology officer, lead a world-wide operation that has delivered an advanced hydroponic nutrient film technique (NFT) growing system to commercial greenhouse growers in more than 20 countries during the last 15 years. The patented Green Automation technique is optimized for lettuce and herb production for larger greenhouse operations (minimum 1 acre). This high-tech, efficient growing method addresses the numerous challenges that entrepreneurs, investors and greenhouse growers encounter, such as:
- Unpredictable weather
- Shortage of labor
- Carbon footprint concerns
- Water shortages
- Consumer demand for local produce
- Crop contamination due to pests
- Human hand product handling
- Inefficient shipping
Recently, the company responded to the ever-growing consumer and investor demand in North America with the introduction of its subsidiary, Green Automation Americas LLC. In the U.S., these growing systems are presently operating in Massachusetts (Little Leaf Farms); New Hampshire (lēf Farms), and New York and Illinois (Gotham Greens). The size of each of these growing facilities ranges from 1 to 3 acres.
Sustainable Indoor Farming
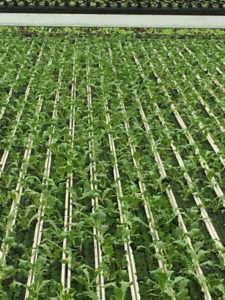
So, what exactly is sustainable indoor farming? According to Patrik Borenius, who manages Green Automation Americas, headquartered in Wellington, Florida, “Simply put, efficiency is the key to sustainable indoor farming. The Green Automation system is designed to produce more, while using less resources — less energy, less space and less labor.”
Borenius details below just how the system is designed for the upmost in energy, space and labor efficiency:
Energy efficiency. Designed for greenhousesthat use natural sunlight as the primary energy source, the leafy greens will all be equally exposed to the enriching rays of the sun during the day, and — thanks to adjusting gutters — no plant shadows another plant. Additional growing lights are only used to supplement the natural light when needed.
Space efficiency. High building costs as well as the revenue needed to facilitate heating every square inch of a greenhouse to maximize the number of plants per area is extremely important. Green Automation uses a patented gutter design in combination with a sophisticated moving gutter system, which makes efficient use of the total growing area. The amount of lettuce produced on 1 acre of this system is equivalent to more than 50 acres of an open-field farming system, and achieves multiple times the yield of a system utilizing non-automated gutters or floating rafts, which are commonly used in greenhouses.
Labor efficiency. The systems minimize excessive labor requirements by using conveyor belts, turntables and lifts, all managed by anadvanced control system. In the case of the “fully automated system,” no human hand encounters the lettuce from start to finish in the entire growing process, from seeding to harvesting. This eliminates any contamination risk and lowers labor costs significantly.
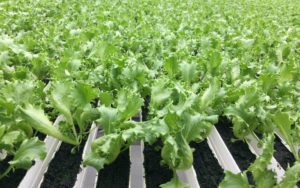
Fully Automated From Seeding to Harvesting
The company offers two automated growing systems — one for living lettuce or head lettuce and one optimized for baby leaf lettuce production. Both systems can be automated from medium filling and seeding to harvesting. The annual yield per square foot of growing space depends on the lettuce variety grown and ranges from over 12 Ibs/sq. ft. for baby leaf lettuce to up to 25 Ibs/sq. ft. for head lettuce.
Follow the process from seed to harvest using the fully automated system and note the elimination of the need for wide walkways throughout the greenhouse, making efficient use of space to allow for growing!
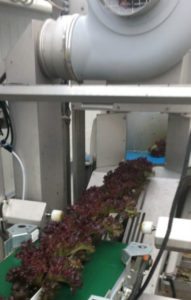
1. Patented narrow gutters are automatically filled with either rock wool or peat and then transported on conveyor belts to the seeding machine. Controlled by software (see Figure 1), the seeds are placed in the gutters at the optimal distance depending on lettuce type.
2. The gutter progresses into the growing space by conveyor belt and turning table. During the germination phase, the plants do not require light and will be placed on the lower level in the growing area.
3. After three to four days, each gutter is lifted into the sunlight by automated elevators. No transplanting is needed as the seeds have been placed directly in the open gutter and grow there until the plants are ready to be harvested. The gutters with the seedlings are starting their journey through the greenhouse right next to each other, using every inch of space in the greenhouse (see Figure 2).
4. As the plants grow they are moved automatically through the greenhouse toward the harvesting area. This automatic gutter movement adjusts the distance between the gutters giving each plant as much space as necessary, but as little as possible, making sure that the growing area is fully utilized (see Figure 3). All plants receive the maximum amount of natural sunlight in the greenhouse.
5. After 14 to 30 days, the lettuce is ready to be harvested. The gutter is transported by conveyor belt to the harvesting area and guided into the cutting machine for a fresh cut and then onto the product packaging area (see Figure 4).
6. After the harvesting process is complete, the medium is automatically removed from the gutter and thoroughly washed. It is once again set to be filled with medium and seeds to start the process again.
Minutes after growing in the greenhouse, the freshly harvested lettuce is ready for delivery to awaiting local grocery stores and restaurants.