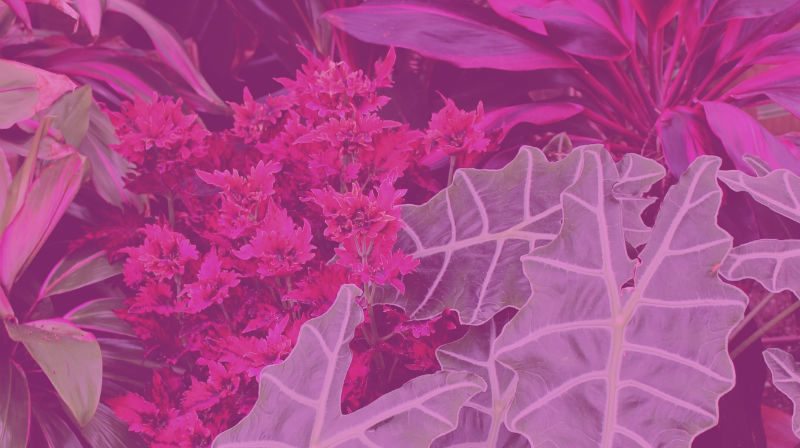
Building a Smart, Sustainable Greenhouse
What if your greenhouse could generate enough electricity to run the equipment used in it, including fans, soil mixers, pot fillers and transplanters? How much money could you save annually in energy costs?
Michael Loik, professor in the environmental studies department at the University of California-Santa Cruz, is studying greenhouse glazing that can generate electricity.
“The purpose of this Wavelength-Selective Photovoltaics Systems (WSPS) technology is to reduce the electricity demand from the grid by generating it onsite,” Loik says. “The footprint of the greenhouse has dual uses. It can grow edible or ornamental plants, and at the same time it’s generating a portion of the electricity required to operate the greenhouse. In the greenhouse in which we were doing the study, more electricity was generated than was needed to operate the fans and the other electrical components.”
“Since we are located along the Pacific coast the cooling demands during the summer are not as high as a greenhouse that would be located further inland. The excess electricity that we generated with our test greenhouse may not be realized everywhere depending on geographic location, how hot it gets in a particular location and the electrical demand required to cool a greenhouse.”
The test greenhouses are covered with single-wall acrylic panels that are embedded with a luminescent magenta dye using a proprietary process. The dye absorbs sunlight and transfers the energy to narrow photovoltaic strips that generate electricity.
“We have been using acrylic panels, which are easy to obtain and relatively inexpensive,” Loik explains. “The dye could also be embedded into polycarbonate panels, which are better at resisting deterioration from the ultraviolet light of the sun. The dye can also be used with glass.”
Loik says glazing embedded with the dye has been extensively tested by its developers Sue Carter and Glenn Alers under extreme conditions including heat, humidity and light levels. Carter and Alers, who are physics professors at the University of California- Santa Cruz, founded the company Soliculture in 2012 to market the technology.
“Plastic panels embedded with the dye were exposed to temperature extremes of 185° F and -40° F and 85 percent humidity,” Loik says. “The panels were also exposed to excessive ultraviolet light at 122° F and worked just fine. There wasn’t any type of breakdown by the dye.”
Loik said whether a grower would decide to put the dye-embedded panels on the greenhouse roof as well as the sidewalls would depend on the orientation of the structure and its geographic location.
“If the wide sides of the greenhouse were facing the sun in the early morning and late afternoon, it might be worthwhile for a grower to install the panels
on the sidewalls to generate some extra electricity,” he says.
Variable Plant Response
Loik studied the effect that light transmitted through the magenta- colored panels had on plant photosynthesis and growth. Twenty different plant varieties, including basil, tomatoes, cucumbers, peppers, strawberries, lemons and limes were trialed.
“We grew plants in greenhouses covered with clear acrylic panels and compared the growth to plants in a greenhouse with the magenta-colored panels,” Loik says. “Eighty percent of the 20 different varieties that we tested basically grew the same regardless of the panel color. The other 20 percent of plants under the magenta-colored panels had a higher photosynthetic rate. Plants that had a higher photosynthetic rate included Roma tomato, a strawberry variety and different varieties of peppers and lemons. In this particular study we did not measure whether the plants produced more fruit or larger fruit. We have also done lettuce and cucumber varieties in other trials and they all grew the same regardless of the panel color.”
“We also found that there was a 5 percent water savings for tomatoes grown under the magenta-colored panels. We are currently conducting more detailed experiments to try to figure out why there is this water savings and also why in some cases there is a higher photosynthetic rate.”
Expected Payback and Potential
Loik says his colleague and panel developer Glenn Alers has done some computations related to expected payback for installing the WSPS technology.
“It depends on whether a grower is building a new greenhouse or is retrofitting an existing structure,” Loik says. “If the panels and all of the hardware including the clips and wire for the voltaics are considered, the cost is about $22 per square foot. For California, when the panel efficiency and the amount of sunlight are considered, the payback is between four to seven years.
“In a research article (http://onlinelibrary.wiley.com/doi/10.1002/2016EF000531/full) published in “Earth’s Future,” we show a graph of the electricity production in the greenhouse over the course of a year. Electricity production was the lowest during December when it was generating about 1⁄2 kilowatt per hour. In June and July when the sun is the highest in the sky, the greenhouse was generating 10 times that much electricity. That is the seasonality part of this technology.”
Loik says the magenta-colored panels have the potential to allow growers to retrofit their greenhouses so they become more efficient.
“Theoretically, a greenhouse could produce more electricity than what would be needed by the greenhouse to operate,” he says. “The greenhouse would be producing more electricity at certain times of the year than others. In some locations it might be possible for growers to sell electricity back to the grid.”
Loik says whether or not this technology lends itself to energy rebates would depend on a greenhouse’s location and the utility company a grower is working with.
“What I would like to see is using this technology as a springboard toward more energy-efficient greenhouses in ways other than just energy,” he says. “With the preliminary water savings that we have seen, it may be possible to combine the dyed panel technology with the small water sensors that are now available. By combining the panel technology with temperature and water sensors it may be possible to specifically determine what plants need to avoid wasting energy and water. This could lead to the creation of a smart, sustainable greenhouse environment.”
For more information: Michael E. Loik, University of California, Environmental Studies Department, Santa Cruz, California; 831.459.5785; mloik@ucsc.edu.