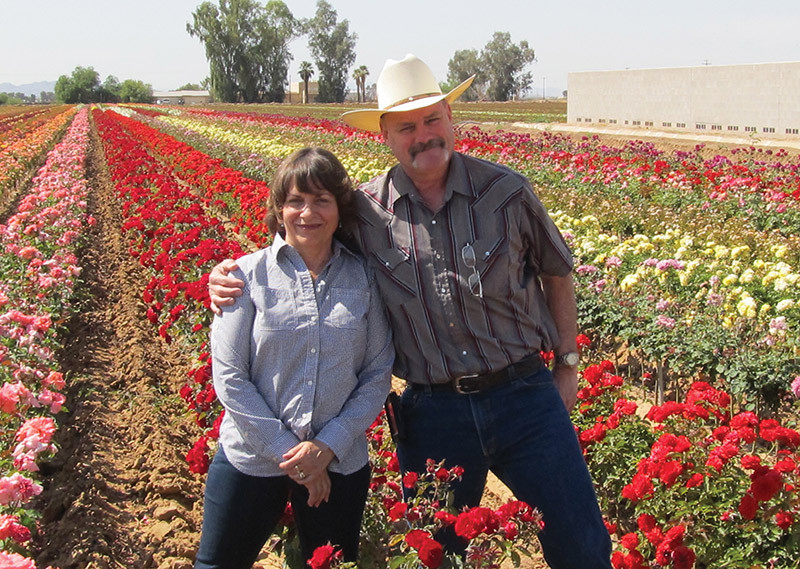
Maintenance, Sanitation and End-of-Year Cleanup
OK, I’ve brought this up throughout the year at different times and you will always hear Ann talk about just how important sanitation is in disease prevention and control.
I think most of us know how imperative it is to keep everything that requires maintenance, maintained. Unfortunately, for some of us it seems like the thought is, “It’s not mine, it’s the company’s. I’m not going to worry about it, I don’t have the time.”
That’s a sad mindset. I think it is part of each of our responsibilities to help keep things clean, in shape and in good working order. Back in my machining days we never got into trouble or asked “Why?” when we turned something into maintenance to get fixed. On the other hand, we did get asked “Why not?” if we didn’t.
Sanitation … yeah what about it? How many of us are on top of sanitation? Sure it’s not always easy; production always wins. Keeping your work area clean is the best way to be able to spot a problem early. If you wait until something emerges from a mess, it is likely that the level of the problem is very high. One of the best ways to keep costs down is to make sure problems are spotted when they are slight and tossing a few plants is the extent of the control strategy. If you do wait until things are obviously falling apart, you will undoubtedly be applying a lot of chemical sprays with the added costs including more labor. And the result is often very expensive waste, which will then be thrown away.
For another thing, if you do not remove dead plants from production you end up spreading disease throughout the crop. Furthermore, you cannot tell if a fungicide works or not since the entire planting still looks bad.
Look Around
If you do nothing during periods of heavy production, what about at the end of the year when times are slow and just about everyone is on vacation or gone for the holidays. As I said before, try taking a different stance. Walk your whole facility and look at it like a customer would. Try sitting on the other side of your desk, look around, look up, see those nasty cobwebs that you normally don’t see. See what they would see and rest assured they will leap to a conclusion about the quality of plants you are offering them.
Think about carpet cleaning, windows, tile floors, bathrooms, offices in general … including yours. As stated above, your customers will take away first appearance issues and most will include those in future decision making. I know I do!
Now’s the time to bring in the pressure washers and let them do their job. Hit the walls, under benches, top and bottom of benches; if you have storage cabinets on the side line in your greenhouse, pull them out and clean behind. This is a great time to use cleaning and sanitizing products when there are few plants and people to work around. Clean all the important OSHA/state-required posters for employees. I’ve been in some places where the dust seems like it has collected on them for years. Get new ones to stay up to date and in step with regulations.
Does anything else need updating? Now might be the time to do it. Look at all your hoses and nozzles — do any need replacing? Check greenhouse cooler filters and pads, office air conditioner/heater filters, ATVs, tractors, carts, etc. Even all the regular vehicles — when was the last time any were serviced?
Start a list and even have your employees go through and add to it; then in December when things have settled down you can start your annual upkeep process. If you have any accumulated junk piles, such as old dirt/media, get rid of it. Look into getting one or more (if needed) of those Waste Management bags that you can fill and they come and pick it up.
Just about most of what we’ve discussed is more on the labor side than spending big bucks to have something done. We understand the value of money, but this is one of those necessary evils that we all have to face and should deal with. There have been a lot of greenhouses that we’ve been in, huge, big and smaller. Same rules should apply to all.
Chase Agricultural Consulting, LLC was formed at the end of 2011 when Ann (A.R.) Chase and Mike Zemke moved to Arizona. Ann has more than 35 years experience in research, diagnostics and practical consulting in plant pathology. She has been retired from the University of Florida – Mid Florida Research and Education Center in Apopka since 1994, but remains on staff as a Professor Emeritus. Mike holds an Associate of Applied Science in manufacturing drafting. Mike started his education in horticulture when he and Ann were married in 1995. He specializes in communications of all sorts within the industry.